Common Investment Casting Defects
There are four main categories of investment casting defects:
Hot Tear or Shrinkage Cracks
This defect occurs when the shell mold restricts the molten metal from contracting during cooling or solidification. These imperfections materialize as jagged cracks. Experienced foundries eliminate these defects by reducing the “strain rate” by preheating molds, using venting holes, and choosing the right type of metal for the project.
Inclusions
This issue describes small, round, or irregular craters and results from foreign on-metallic particles in the casting. They may also look like depressions in a variety of shapes and sizes. A reputable metal casting foundry will ensure that all slag particles are removed from the molten metal prior to pouring it into the mold cavity.
Misrun
If the molten metal doesn’t completely fill the mold cavity, this defect can happen. It’s most attributable to the shell being too cold, the fill rate being too slow, or a faulty design mold. Work with a foundry that is known for delivering quality mold making services to avoid misruns.
Porosity
This defect includes the formation of bubbles within the investment casting during the cooling phase. Liquid materials contain dissolved gas, and, when expelled, these bubbles form. With the right equipment, investment casting foundries can prevent porosity defects.
Preventing Defects: Using Ultrasonic Flaw Detectors
The investment casting process is complex and rife with opportunities for irregularities. Reputable foundries will invest in the best equipment and technology to analyze production quality and accuracy.
Ultrasonic flaw detectors are modern-day reflectoscopes used to identify defects in prototypes. It can discover various defects, including cracks, inclusions, voids, shrinks, porosity, flaking, and other subsurface imperfection.
How a Flaw Detection Works
Pulse echo instruments can work in two ways: straight beam testing and angle beam testing. Straight beam testing detects flaws parallel to the plane of the part. Angle beam testing offers more detail. It can identify defects at angles and other areas not reachable by straight beam testing. It can also find issues in the parent metal from welds.
Flaw detection is important for every industry, but it’s critical for aerospace investment castings and automotive casting services.
Investment casting is a widely used manufacturing process that is employed to create complex parts with high dimensional accuracy. However, despite its popularity, investment casting is not free from defects. Investment casting defects can lead to significant losses in time, money, and resources, and can even compromise the safety of the end-product. For this reason, it is crucial to take preventative measures to minimize the occurrence of defects.
There are several common types of investment casting defects that can occur during the manufacturing process. These include shrinkage, porosity, cracks, and distortion. Shrinkage occurs when the metal cools and contracts, resulting in a reduction in the overall size of the part. Porosity is caused by gas pockets that form during the solidification process, while cracks can occur due to thermal stresses or other factors. Distortion can result from uneven cooling or from the release of residual stresses in the part. By understanding the causes of these defects, manufacturers can take steps to prevent them from occurring.
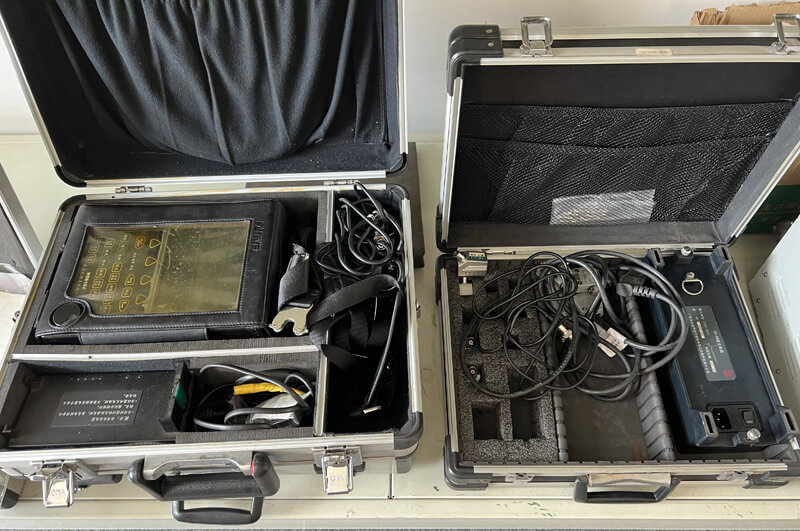
Common Defects
Investment casting is a complex process that requires precision, attention to detail, and a thorough understanding of the materials and techniques involved. Despite the best efforts of manufacturers, however, defects can occur during the casting process, leading to wasted time, materials, and money. Some of the most common defects in investment casting include shrinkage porosity, gas porosity, and cold shut.
Shrinkage Porosity
Shrinkage porosity is a type of defect that occurs when the metal in the casting shrinks as it cools, creating small voids or holes in the material. This can happen when the casting is too thick or when the metal is not properly distributed throughout the mold. Shrinkage porosity can be difficult to detect, as the voids are often very small and can be hidden beneath the surface of the casting.
To prevent shrinkage porosity, manufacturers must carefully control the temperature and pressure of the casting process, ensuring that the metal is distributed evenly and that the casting is not too thick. They may also use additives to improve the flow of the metal and reduce the risk of shrinkage.
Gas Porosity
Gas porosity is another common defect that occurs when gas bubbles become trapped in the metal during the casting process. This can happen when the metal is not properly degassed, when the mold is not properly vented, or when the metal is poured too quickly. Gas porosity can weaken the material and make it more prone to cracking and other types of damage.
To prevent gas porosity, manufacturers must take steps to ensure that the metal is properly degassed before it is poured into the mold. They may also use vents and other techniques to allow trapped gas to escape from the mold, reducing the risk of bubbles forming in the metal.
Cold Shut
Cold shut is a type of defect that occurs when two streams of metal meet in the mold but fail to fuse together properly. This can happen when the metal is poured too slowly or when the mold is not properly designed. Cold shut can weaken the material and make it more prone to cracking and other types of damage.
To prevent cold shut, manufacturers must carefully control the speed and temperature of the casting process, ensuring that the metal flows evenly and fuses together properly. They may also use additives to improve the flow of the metal and reduce the risk of cold shut.
Preventative Measures
Wax Injection
To prevent defects in investment casting, proper wax injection is critical. Wax patterns must be produced with precision to ensure that they are dimensionally accurate and free from defects. The following preventative measures can be taken during wax injection:
- Use high-quality wax that is free from contaminants and has consistent properties.
- Keep the wax at the proper temperature and viscosity.
- Ensure that the injection pressure is consistent and that the wax flows smoothly into the mold.
- Use high-quality injection equipment that is properly maintained.
Shell Building
The shell building process is another critical step in preventing investment casting defects. The following preventative measures can be taken during shell building:
- Use high-quality refractory materials that are free from contaminants and have consistent properties.
- Ensure that the shell thickness is consistent and that there are no thin spots or voids.
- Use proper drying techniques to prevent cracking or warping of the shell.
- Follow proper storage and handling procedures to prevent damage to the shells.
Dewaxing
Dewaxing is a critical step in the investment casting process that must be done carefully to prevent defects. The following preventative measures can be taken during dewaxing:
- Use proper dewaxing equipment that is properly maintained and calibrated.
- Use the proper dewaxing temperature and time to prevent cracking or warping of the shell.
- Ensure that the dewaxing process is done in a clean environment to prevent contamination of the shell.
Pouring
The pouring process is the final step in the investment casting process and must be done carefully to prevent defects. The following preventative measures can be taken during pouring:
- Use proper pouring techniques to prevent turbulence and ensure that the metal flows smoothly into the mold.
- Use proper gating and risering techniques to ensure that the metal fills the mold properly and that there are no defects in the casting.
- Use high-quality metal that is free from contaminants and has consistent properties.
By taking these preventative measures, investment casting defects can be minimized, resulting in higher-quality castings that meet customer specifications.
Inspection and Quality Control
Investment casting defects can be prevented through proper inspection and quality control measures. Inspection and quality control are essential to ensure that the castings meet the desired specifications and are free of defects. The following sub-sections discuss the different methods of inspection and quality control that can be used in investment casting.
Visual Inspection
Visual inspection is the most common and basic method of inspection used in investment casting. It involves a thorough examination of the casting surface to identify any visible defects such as cracks, porosity, surface finish, and dimensional accuracy. Visual inspection can be performed using the naked eye or with the help of magnifying tools such as microscopes and borescopes.
Radiographic Inspection
Radiographic inspection is a non-destructive testing method used to detect internal defects such as porosity, cracks, and inclusions. This method involves the use of X-rays or gamma rays to create a radiographic image of the casting. The radiographic image is then examined for any defects. Radiographic inspection is a highly effective method of inspection but requires specialized equipment and trained personnel.
Dimensional Inspection
Dimensional inspection is used to ensure that the casting meets the desired dimensional accuracy. This method involves the use of measuring tools such as calipers, micrometers, and gauges to measure the casting dimensions. Dimensional inspection is critical to ensure that the casting fits correctly and functions as intended.
In conclusion, inspection and quality control are essential to prevent investment casting defects. Visual inspection, radiographic inspection, and dimensional inspection are the primary methods used to ensure that the castings meet the desired specifications. By implementing these methods, manufacturers can ensure that their investment castings are of high quality and free of defects.
Quality Equipment Is a Top Priority
When choosing a foundry for investment casting, make sure they have a defect prevention process. In our investment casting services, we use a variety of equipment, including an ultrasonic flaw detector, to prevent defects. With our own dedicated mold shop, our customers receive quality, accurate, and consistent productions.
Conclusion
In conclusion, preventing investment casting defects is crucial to ensuring the quality and reliability of cast parts. By following the best practices outlined in this article, manufacturers can significantly reduce the risk of defects and improve their casting yield.
One of the most important steps in preventing investment casting defects is proper mold design and preparation. This includes selecting the right mold materials, ensuring proper gating and risering, and using appropriate coatings and binders.
Another critical factor is maintaining the correct casting parameters, such as temperature, pressure, and cooling rates. This requires careful monitoring of the casting process and making adjustments as needed to ensure consistent results.
In addition, manufacturers should also implement rigorous quality control measures, such as visual inspection, non-destructive testing, and mechanical testing. This can help identify defects early on and prevent them from causing further issues down the line.
Overall, preventing investment casting defects requires a combination of careful planning, precise execution, and ongoing quality control. By following these guidelines, manufacturers can produce high-quality cast parts that meet the most demanding specifications and requirements.